manufacturing process
rack
The rack method is typically used to process large,complex part configurations. These components are individually wired and suspended on a picture frame holding device. This prevents potential collisions and subsequent damage during the plating process. Plating is deposited through the use of external anodes tied to an independent power source. This enables the metal deposit to be applied consistently and evenly over the surface of the part. The principal advantage of the rack method is to deliver a precise plating deposit on intricate part geometries and avoid potential damage caused by other "mass" processing techniques. The rack method is also deployed to selectively deposit metal on designated areas of the product.
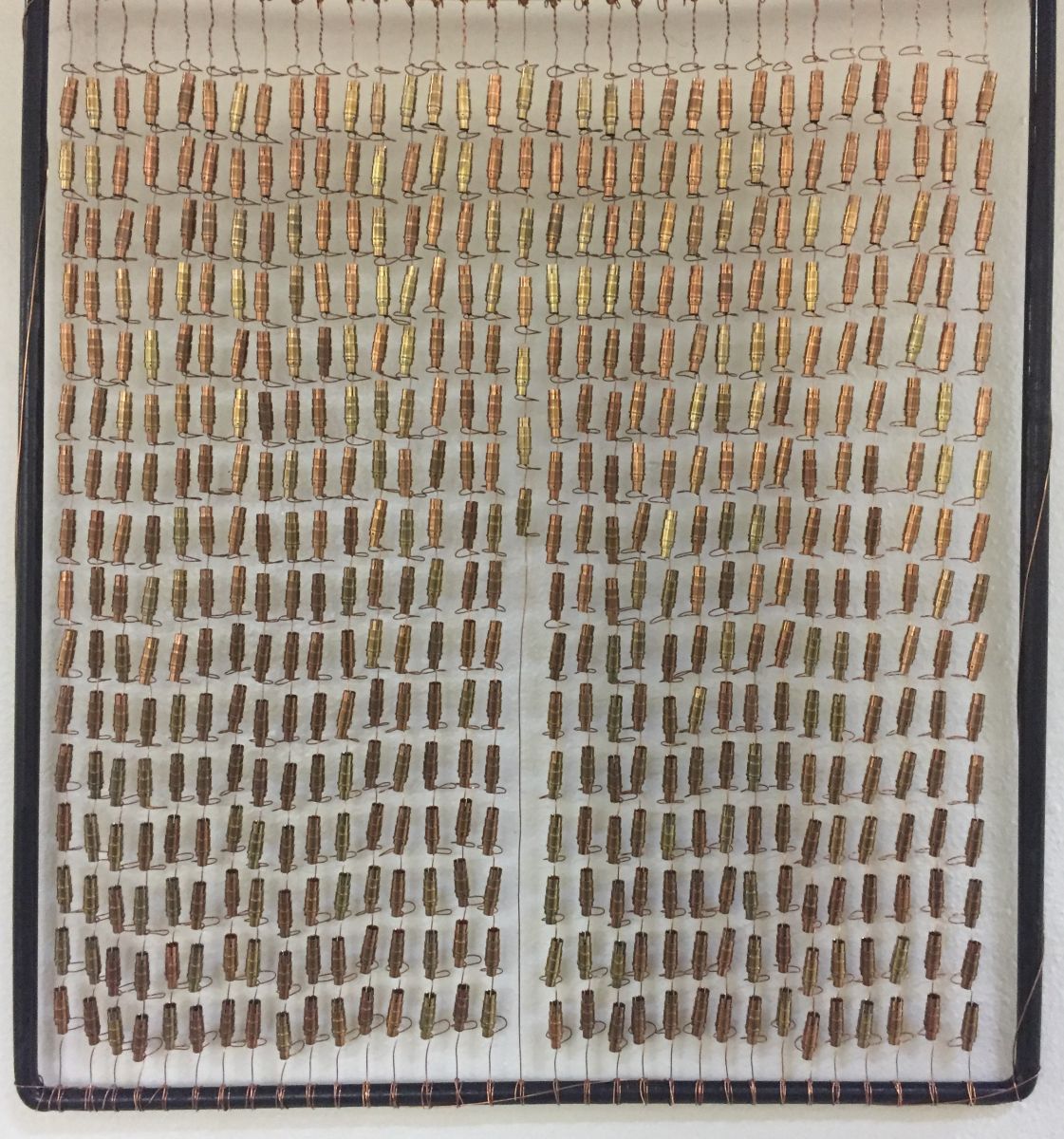
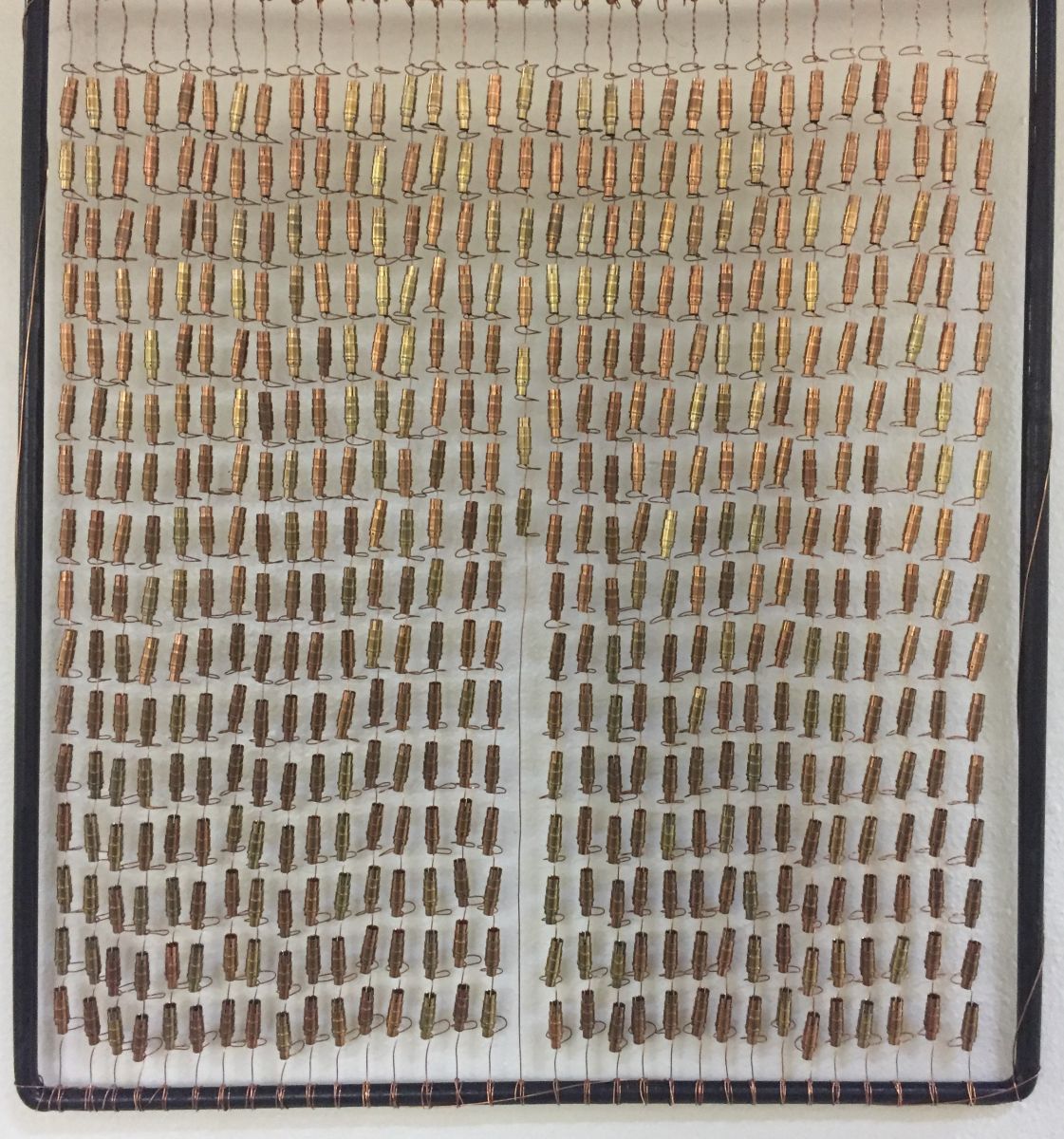
barrel
Component parts are placed inside a fine mesh barrel that slowly rotates while immersed in the plating tank. The metal is deposited by distributing electrical current through the use of center bars and danglers within the bath. The tumbling action agitates the parts and insures a uniform metal thickness without damaging the component features. Optimum barrel load sizes, the addition of plating media, in-process audits and precise electro-chemical formulations all contribute to high quality results. The barrel process is considered the most efficient and cost effective method for plating small geometry parts.
vibratory
This method is best suited for delicate, fine geometry parts with small inside diameters, threads, or blind holes. Fragile parts with tiny features are the best candidates for this process. Components are loaded into a spiral cylinder and are subject to a light, gentle agitation to evenly deposit the metal. The primary benefits include excellent plating uniformity, avoidance of damage during the plate process, and the capability to deposit metal in the most difficult areas of the component.
continuous
Cal Aurum specializes in the short run processing of gold plating for wire and ribbon from 50-20,000 feet. We can process wire sizes of 18-40 AWG and ribbons from .0015 X .002 to .004 X .500 inches. Our flexible processing line can handle your short run requirements with quick turnarounds and minimal raw material capital outlay.